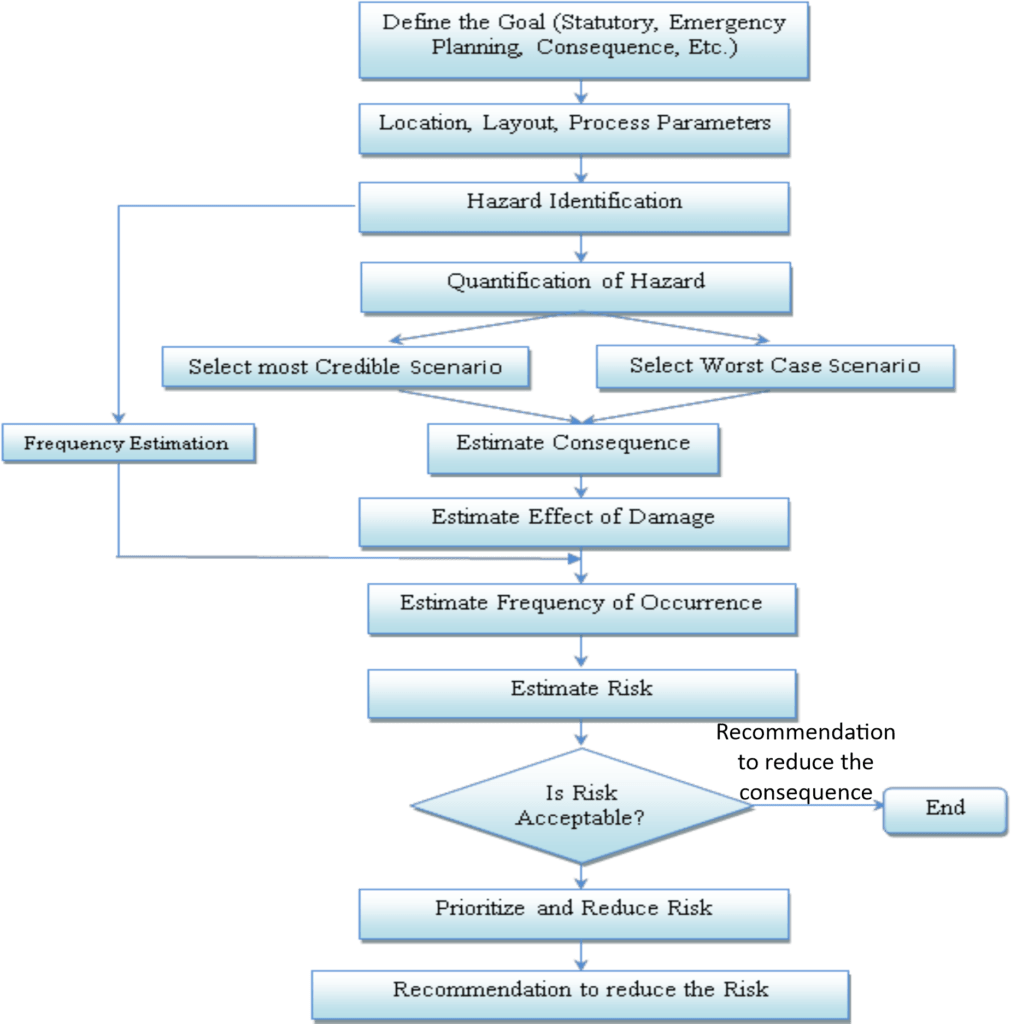
WHAT IS PST?
- Process Safety Time (PST) is a Period of time between a failure occurring in the process or the process control system and the occurrence of the hazardous event if the safety function is not performed.
- For example, When a the flow rate through a compressor becomes very low, material can back through the compressor causing it to ‘surge’. In this case, the “process safety time” is the time interval between when a low flow alarm is received and when the compressor actually surges.
- In simple words, it refers to the period of time between a failure, that has the potential to give rise to a hazardous event, occurring in the EUC .[equipment under control] or EUC control system and the time by which action has to be completed in the EUC to prevent the hazardous event occurring.
WHAT ARE REQUIRED?
- PST requires process variable that is most closely associated with the occurrence of the hazardous event,
- It considers the time of the hazardous event or the point at which the hazard can no longer be reliably prevented.
- It also includes the known design limit of the equipment conservatively associated with the process equipment.
WHY PST IS IMPORTANT?
- It determines the maximum amount of time that can be allowed for the Safety Instrumented System (SIS) to perform.
- Determination of PST is the first step in identifying the time potentially available for all protection layers to respond and will be useful in specifying the required response time of each.
- It prevents the development of unmitigated hazard scenarios and provides a particular protection layer in process plants.
ACTIONS PERFORMED BY SIS
- Sense the out-of-control condition.
- Digital filtering of input signal.
- Input process scan time.
- PLC program scan time.
- Any trip delay timers set to remove process noise must time out.
- Output process scan time.
- Digital filtering of output signal.
- Fully actuate the output device.
HOW PST IS DETERMINED?
- The upper limit of normal operating conditions and the Maximum Allowable Working conditions of the equipment must be used to estimate PST.
- The amount of time between these two discrete points in time, initiating event and hazardous event, depends on the estimated rate of change of the process variable due to the initiating event.
- The initial value of the process variable of interest at the time of the Initiating Event (PVIE), the value of the process variable of interest at the time the Hazardous Event (PVHE), the estimated Rate of Change of the process variable of interest under worst-case credible conditions (PVROC). These three variables will be completely dependent upon the specific process, process equipment, and even the mode of operation.
- PST can be estimated by the following formula:
- Once the analysis is complete and PST determined for each scenario, the data and assumptions will be quite useful for subsequent activities and should be maintained as valuable Process Safety Information (PSI).
GUIDE LINES
- Determination of PST supports the claims regarding Functionality, Auditability, and controlled Management of Change as part of a larger effort to validate each of the core attributes of an Independent Protection Layer.
- PST should be evaluated by an individual or team with specific knowledge of the process, process equipment, and its operation.